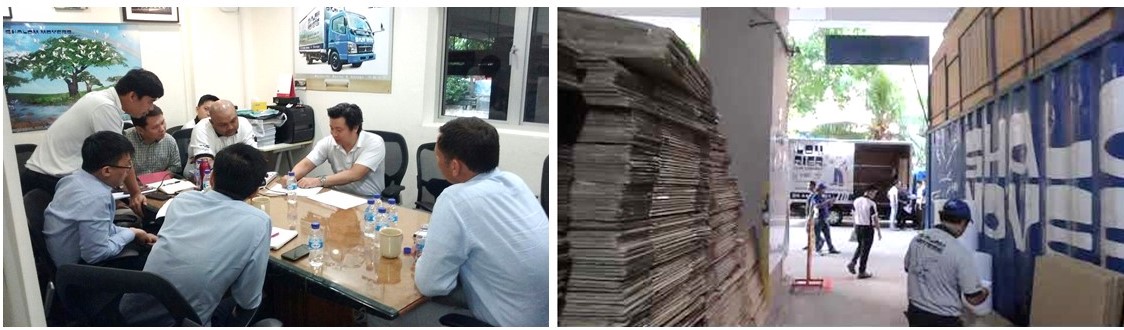
At Shalom Movers, four to five movers are deployed for each moving job. They would wrap, pack and then move the boxes to a holding area near the lift lobby before transporting the boxes to the ground floor to be loaded into trucks. This meant that one person always had to be deployed at the holding area. With one less person, packing and moving the boxes took a longer time.
To solve this issue, the business implemented the “just-in-time” concept: they eliminated the intermediate step of gathering boxes at the holding area and instead transported boxes directly to the truck. They also moved in smaller batches, thus achieving a continuous flow of boxes. As a result, the person at the holding area could be freed up to assist with the workload.
This solution was one of several ideas adopted by Shalom Movers when exploring how to make the work of movers and staff more seamless and less wasteful through Lean Thinking. After all, as a business relying heavily on manpower, Shalom Movers was subjected to increasing operational costs in a tight labour crunch as faced by many small- and medium-sized enterprises (SMEs) in Singapore. Since participating in the Lean Skills Development Programme (LSDP) at SIT in October 2017, the company has accelerated its Lean journey with an aim to improve operational efficiency and upskill its workforce.
Reducing bottlenecks
Besides freeing up capacity of its movers, Shalom Movers further identified issues that were preventing trucks from leaving on time. This is because movers were supposed to be on the road by 8:00 a.m. so as to be able to reach their customers’ premises by 9:00 a.m. sharp. One of its first tasks was to review how it could reduce waste by redesigning operations at its warehouse.
One bottleneck identified was at Shalom Movers’ service counter, where movers made requests for supplies such as cartons, masking tapes and shrink wraps. Movers would also have to wait for their supplies before moving out for the day. As the service counter was located near the storage area, it was often crowded. To ease the bottleneck, the service counter was moved curb-side. The process was also enhanced such that movers could easily request and pick up supplies at the same time and in an organised manner.
Another area of inefficiency was that 30 to 40 movers had to queue every morning at the entrance of the warehouse in order to collect their reimbursements for project claims. This resulted in further delays and congestion in the warehouse. In response, the project team came up with ideas such as limiting the number of people lining up at any one time to five, and providing movers with a card they could hand over to a staff member who handled payments.
Once these changes were implemented, tangible results started to appear. Movers experienced increased productivity and shorter process times instantly. With this quick win, staff were more eager to try out more solutions.
Driving innovation
Since implementing Lean Thinking, staff of Shalom Movers have become more open to suggesting improvements and stepped up to new roles and responsibilities. For example, staff created a bubble wrap transfer machine by repurposing the motor of an old massage chair. The machine helped break down large industrial-sized rolls of bubble wrap into smaller, more portable rolls. This allowed for ease of usage and increased productivity, as well as reduced time lost when the process was done manually.
“The biggest change we have seen as a result of Lean was the mindset shift in our people and their yearning for continuous improvement,” observes Mr Gabriel Lam, Chief Operating Officer of Shalom Movers. According to Mr Lam, it is the strive for continuous improvement that will prove most valuable for the company in the future. He also believes it is one of the reasons behind Shalom Movers being officially recognised as a Great Place to Learn in 2018, Great Place to Work in 2018, and one of Asia’s Best Workplaces in 2019. In July 2019, the company won an award by the Singapore government for Business Excellence Service Quality Class with Innovation and People niches.
“Lean is more than just a productivity improvement exercise,” he continues. “It is a journey towards accountability, clarity over goals and roles, better leadership, and continuous learning. It is about professionalising ourselves, not just about improving productivity. Through Lean, our people have shifted their mindsets towards continuous improvement. Each of them now has a way to tap into his or her full potential to increase productivity and efficiency, channel creativity, and innovate.”
Associate Professor Jawn Lim, SIT, who supported Shalom Movers during its transformation, agrees, “Shalom Movers is the consummate example of applying Lean to every aspect of the company’s processes. They are quick with their PDCA (plan-do-check-act) cycles. Their objectivity in examining their existing conditions, measuring, analysing, and solutioning is really second to none. They have embodied what it means to have the entire organisation thinking Lean.”
Case study adapted from 'The Learning Enterprise: Innovative Practices for Organisational Transformation', a book by NACE@SIT that documents the learning journey of four local companies to pioneer workplace learning and Lean transformation with SIT.